What sets Polyhistor apart from most job shops?
Our custom manufacturing experts are also engineers.
This distinction means you benefit from highly skilled professionals who approach every prototype, part, and product through an engineering lens. We’re adept at identifying design issues, brainstorming solutions, and recommending modifications.
Made by Manufacturers, Optimized by Engineers
Here’s how Polyhistor’s engineers deliver precision machining and product engineering services optimized for exceptional quality and cost.
Intentional tolerances
We frequently manufacture features with precision tolerances—a capability we’ll proudly admit we’ve perfected! However, we also commonly receive designs with tight tolerance callouts that aren’t necessary to the fit or function of the part.
If we discover that you’ve requested precision tolerances unnecessarily, we’ll reach out to you for permission to loosen those tolerances, saving you money and speeding up your delivery timeline.
Minimal waste
Prototyping may result in significant excess material—material you’ve paid for. For example, a prototype may require a material with a $3,500 purchase minimum, even though only 10% of the purchased material will be used. That’s a lot of waste!
Our knowledgeable engineers can recommend material alternatives or design adaptations that enable 10x less waste—all without hindering the prototype’s functionality.
We make similar recommendations to prevent wasted time as well. And since time is money, we’re known for helping our customers reduce manufacturing costs.
End-use consideration
We encourage customers to tell us as much as possible about a part’s end use so we can make the best recommendations.
For example, when a customer supplies us with their assembly files, we can see how the part we’re working on contributes to the functionality of the final product. This insight allows us to identify potential problems and, if needed, recommend adjustments to ensure your application works as intended.
When we know what you’re trying to achieve, we can help you get there!
Engineer approval
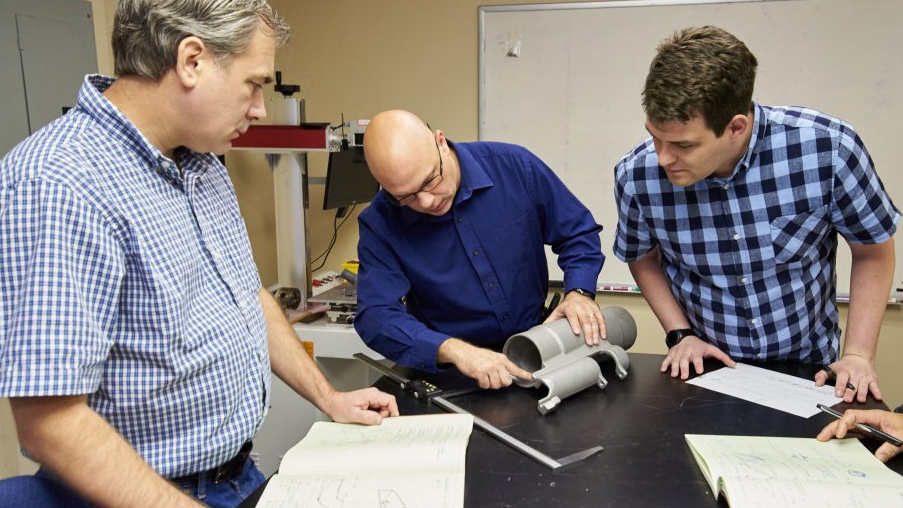
Most machine shops don’t offer in-house engineering services. While such shops can certainly produce excellent parts, your design will likely get manufactured as-is—mistakes and all.
Polyhistor engineers review every design for oversights and errors because we don’t want to waste time or money (yours or ours!) making a product that will only get scrapped due to an easily remedied issue. Count on our team to have your best interests in mind.
Prototype-to-production services
Polyhistor is one of the rare shops offering both product engineering services and high-volume precision machining. With our full range of engineering and manufacturing capabilities under one roof, we can help you develop your product, support you through the prototyping phase, then move your product into full production when you’re ready to launch.
The familiarity we develop with your product, your team, and your goals enables significantly faster production times than you’d get almost anywhere else.
Transparent communication
At Polyhistor, we believe communication is the key to successful product development and manufacturing. If we’re unsure of your intent with a design callout, we communicate with you. If we encounter a challenge that will cause a delay, we communicate with you. And if we discover an opportunity to save you time or money, we communicate with you then, too.
The Polyhistor team is committed to staying in close contact with every customer so you always know the status of your order.
Get your next project off the ground and into production with Polyhistor. Request a quote!