At Polyhistor International, we’re always looking for every possible way to make your project more efficient and cost-effective. It’s part of our collaborative mindset—we view all of our customers as true partners. We’re committed to enabling their success in any way we can, whether through custom order options or design for manufacturing guidance. One behind-the-scenes […]
Blog
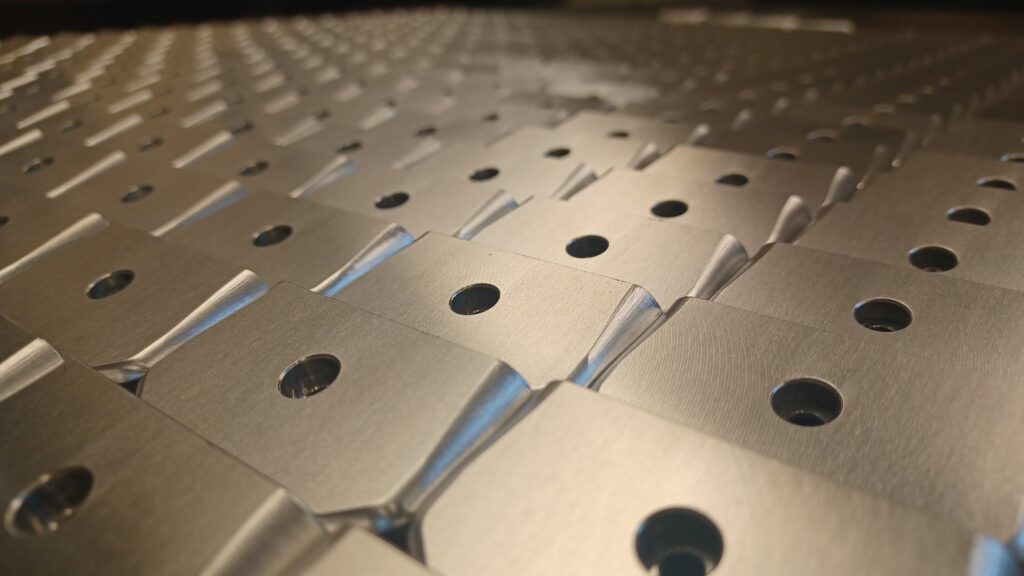
Blanket Orders: Save on Costs and Manage Uncertainty in Your Manufacturing Project
There’s a great deal of uncertainty in today’s economic landscape, and it’s directly impacting the manufacturing industry. Material costs are volatile, and lead times can frequently fluctuate. Smart production planning can now be the difference between an efficient, on-time project and costly delays. How can you ensure your project moves forward smoothly? At Polyhistor International, […]
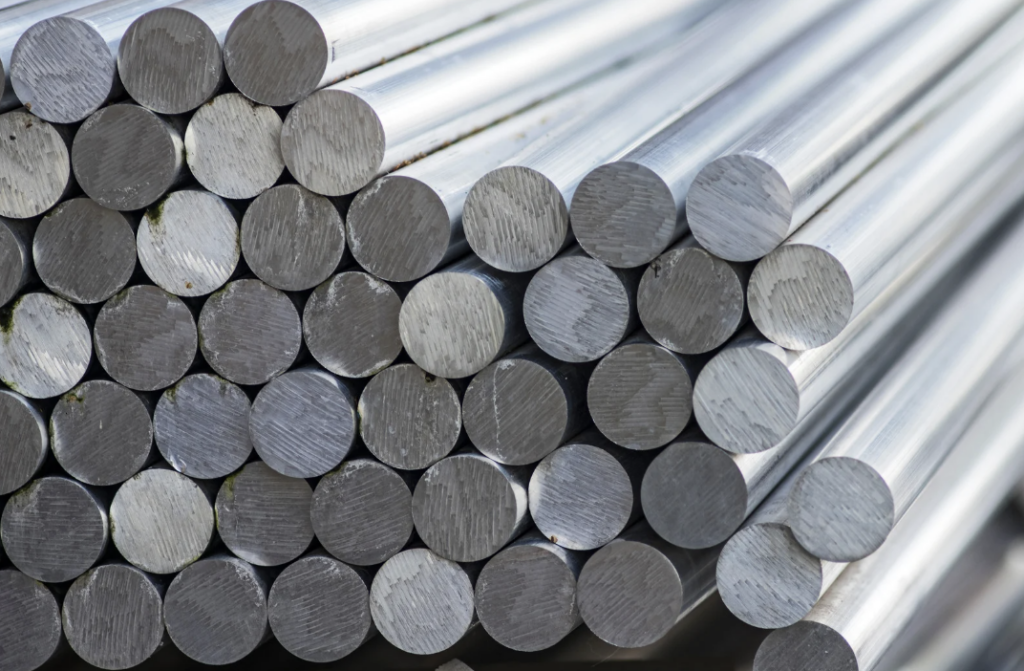
Accelerating High-Volume Machining With Our Equipment and Expertise
As a trusted name in American-made, high-volume machining, Polyhistor International is known for pushing the limits of throughput — without ever sacrificing quality. We’ve earned a reputation for precision and performance among our partners, and we don’t believe in settling for “good enough.” We’ve Invested in What Matters — So You Don’t Have To. By […]
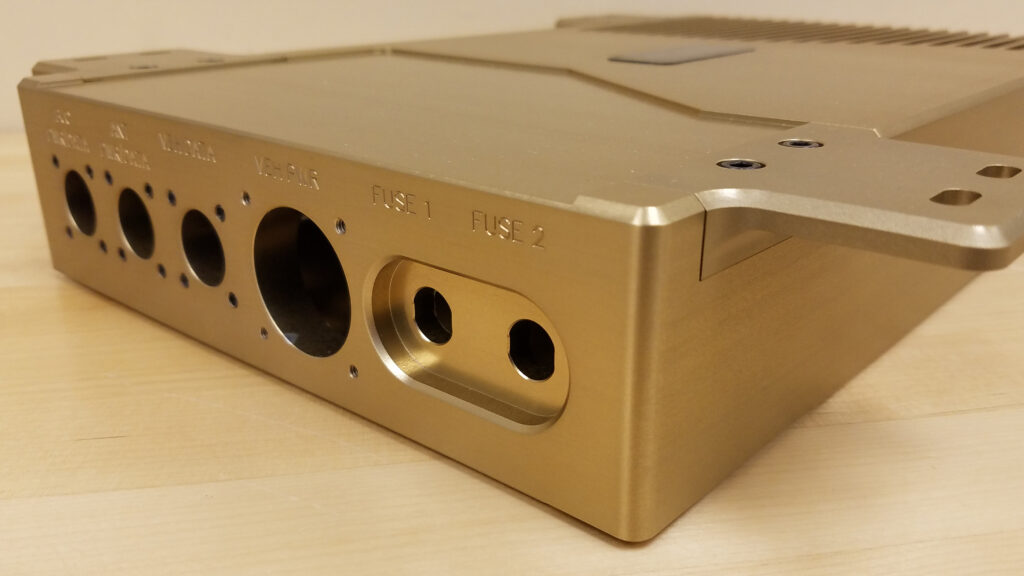
Engineer Defense Enclosures to Withstand Extreme Conditions
At Polyhistor International, our decades as a defense supplier have taught us the challenging conditions mission-critical equipment will face. Products must perform equally well in the scorching desert and frigid Alaskan conditions alike, all while maintaining sealing and protection. When we manufacture defense-grade enclosures in our CNC machine shop, we’re creating shields to protect critical […]
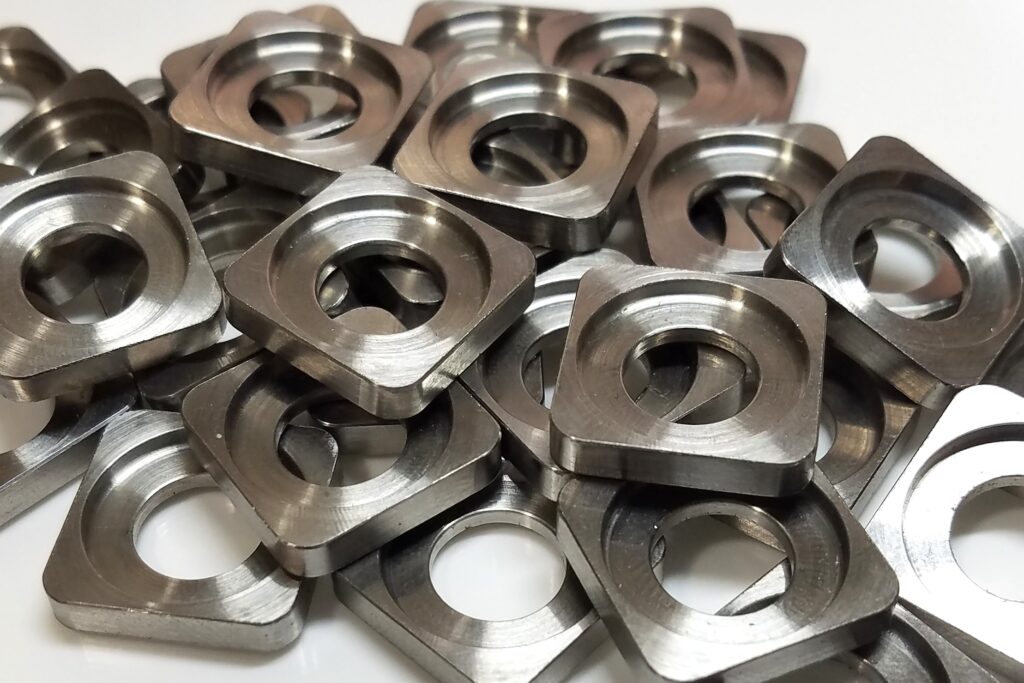
Optimizing High-Volume Production: Strategies for Cost-Efficient Scale-Up
The transition from prototyping to large scale production can be a complex and expensive process for many companies. Without proper planning, decisions that were adequate for the production of a handful of parts will become extremely inefficient for producing thousands. At Polyhistor International, we’re experts in both prototyping and high-volume CNC machining. While many view […]
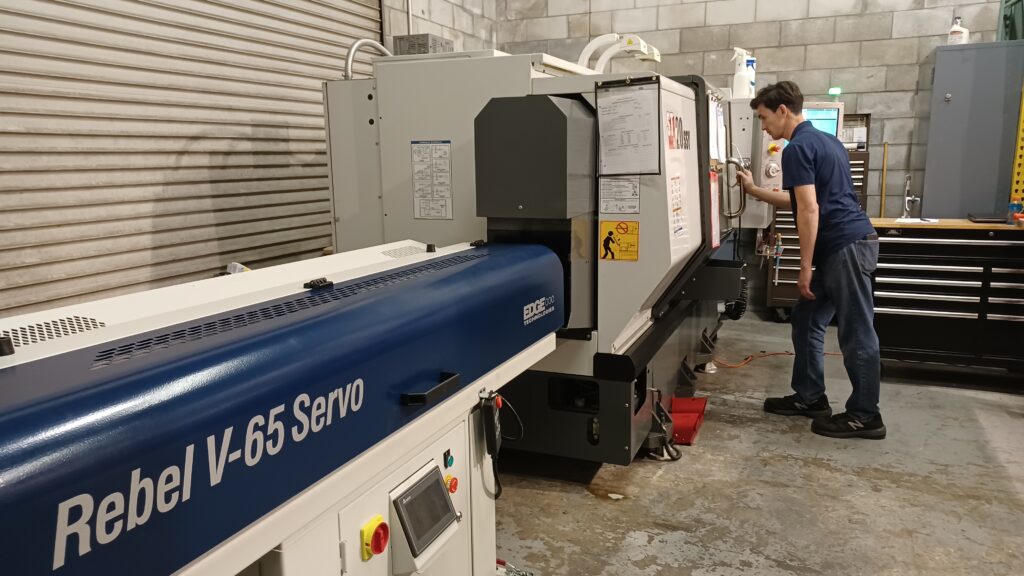
5 Essential Qualities in a Great Manufacturing Partner
The search for a manufacturing partner often begins with metrics like lead time that allow for an easy comparison between suppliers. But after decades in business here at Polyhistor International, we’ve learned that successful partnerships are built on far more than just a single number. Consider the story of one of our repeat customers: they […]
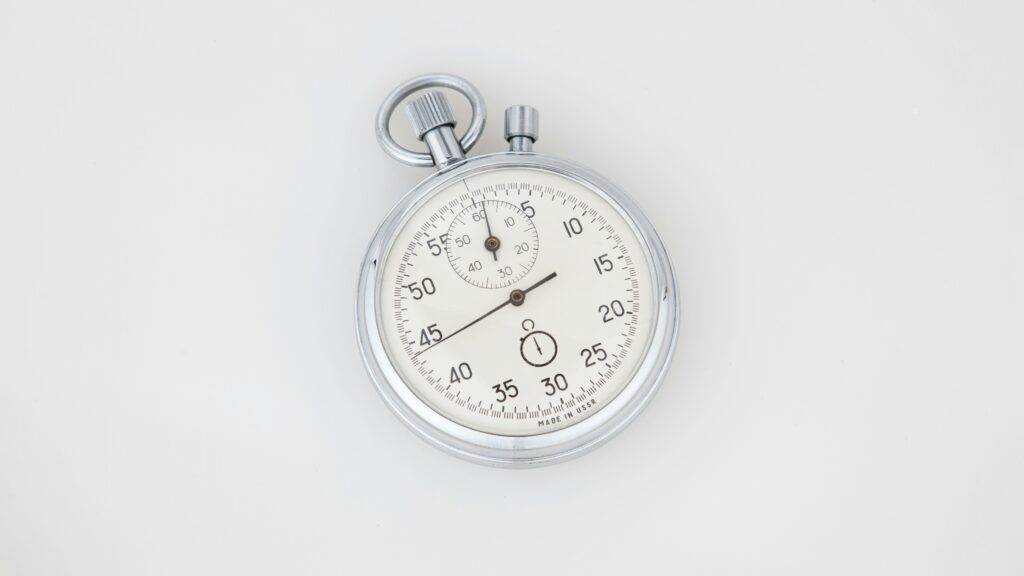
Tackling Tight Deadlines: How Polyhistor Delivered Critical Parts Over a Holiday Weekend
A few years ago, as Independence Day approached, our plans mirrored those of millions of other Americans: We expected a relaxing long weekend full of fireworks and grilling. Suddenly, a defense contractor contacted us with an urgent request: they needed parts within five days—including the holiday weekend. The contractor was a long-time partner, and we […]
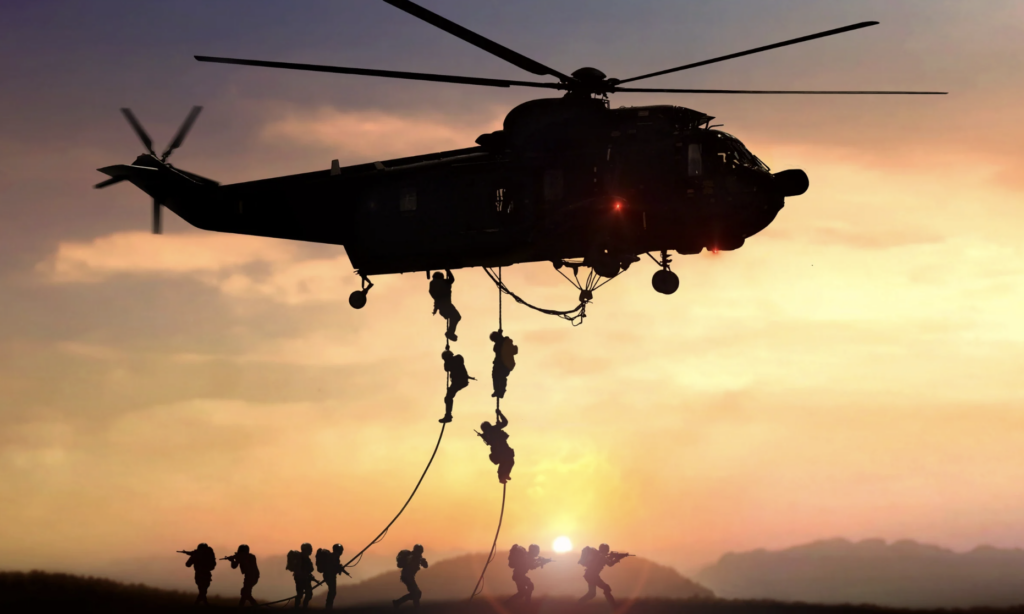
Partnering for Precision: Two Decades of Excellence in Defense Manufacturing
At Polyhistor International, we are proud of our success in partnering with a diverse range of customers. Our ability to assist with product development and our extensive manufacturing capabilities set us apart as a versatile partner to any sector. From medical to lighting, from signage to automotive, we enjoy tackling the challenges that come with […]
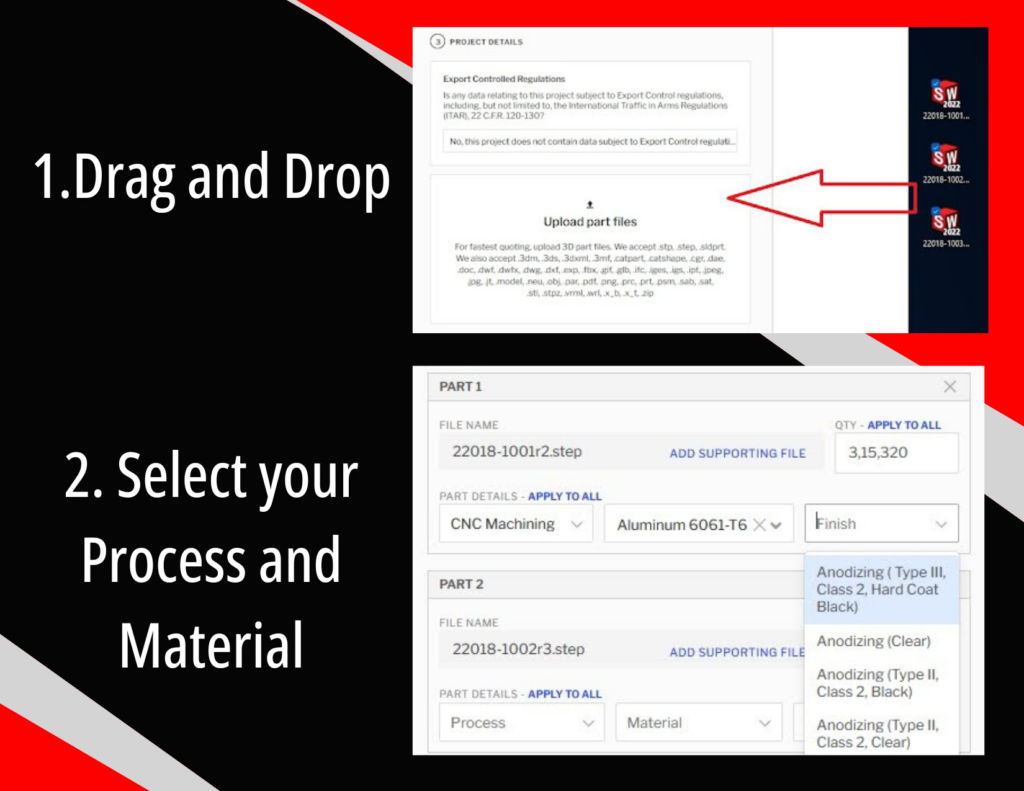
Get Faster, More Accurate Quotes with Polyhistor’s Online Portal
The quoting process may not be the most exciting part of manufacturing, but it’s one of the most critical steps to ensuring project success. At Polyhistor International, we understand how important it is to provide fast, accurate, and transparent quotes to keep your project moving forward. That’s why we’ve developed an online quoting portal designed […]
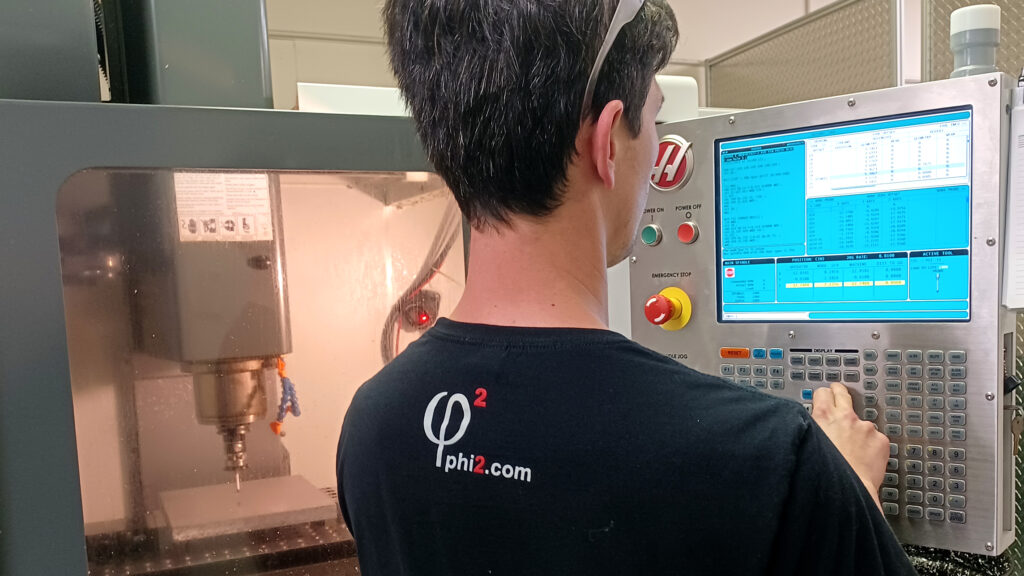
The True Value of Polyhistor as a Manufacturing Partner
At Polyhistor, we believe we’re a bit different from other manufacturers and CNC machine shops. And that difference shows up even in the terminology we use – we like to think of everyone we do business with as our partner instead of just a “customer.” But is there really a distinction, or are these just […]