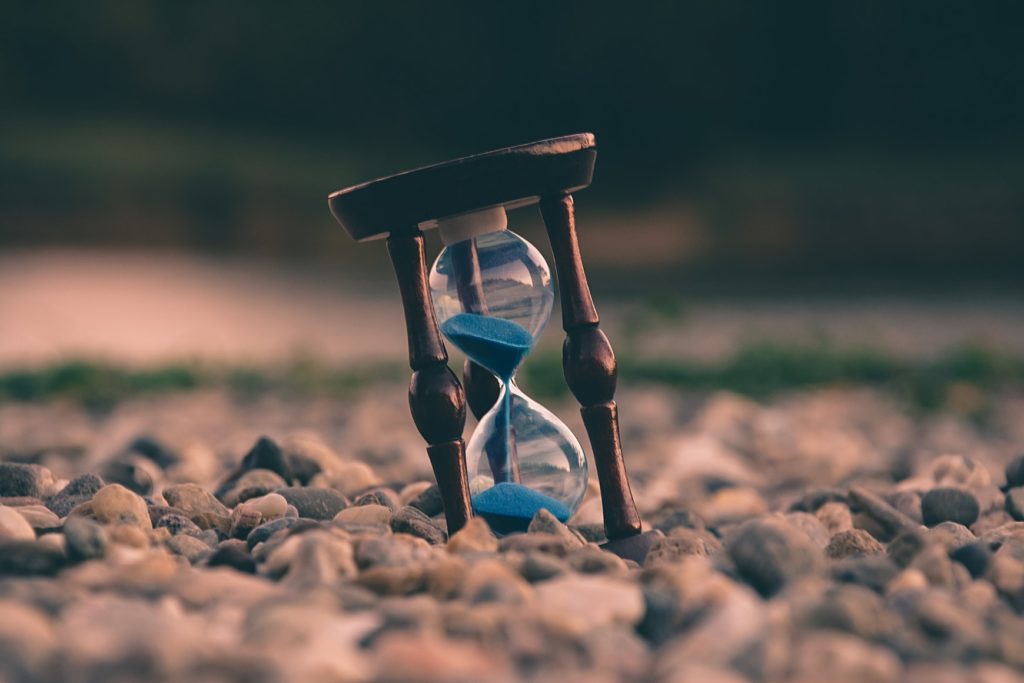
Time is always of the essence in manufacturing. There are so many moving parts involved in bringing a product from concept to completion—and plenty of opportunities for things to go wrong and timelines to get delayed.
It certainly doesn’t help that the manufacturing industry is uncharacteristically volatile at the moment. Global supply chain disruptions and raw materials shortages threaten to derail projects at every turn.
Now more than ever, customers seek assurance from contract manufacturing services providers that they’ll get their parts when they need them. At Polyhistor, we hear your concerns loud and clear. We’re committed to doing whatever it takes to ensure on-time delivery.
How to Avoid Delays in Your Manufacturing Timeline
Let’s look at 5 helpful strategies for optimizing your manufacturing timeline:
1. Don’t release products too early
Sometimes customers are so eager to move into production that they release products before finalizing their designs.
As a team of engineers, we understand the excitement around new product releases! The problem is that accommodating last-minute design changes during production can significantly delay timelines and introduce unnecessary risk into the manufacturing process.
Don’t get us wrong—we honor and appreciate the iterative nature of product development. That’s why we recommend comprehensive prototyping prior to production. In most cases, holding off a little longer on production to finalize a design results in more accurate—and sometimes shorter—overall timelines.
2. Pre-order materials
Material sourcing is a major challenge right now across the manufacturing industry. Expect that the materials for your project will take much longer to arrive than usual.
We prefer to order material ourselves as part of our contract manufacturing services, but we acknowledge that customers sometimes prefer to supply their own.
If you’re going that route, pre-order materials while the products are still in design to avoid potential supply chain delay . Once the design is finalized, we can hit the ground running on production. We may even be able to start machining your parts earlier than anticipated.
One small caveat—when you pre-order material, there’s always the risk of buying less than what you actually need, so be sure to check in with your manufacturing partner to ensure that the quantity you order accounts for any potential design adjustments and/or manufacturing shrinkages.
3. Prioritize communication
Quick and easy communication between customers and manufacturers is key to keeping projects on track.
Many production manufacturers operate at close to full capacity and have their machines prepped to run on a tight schedule. Being available to answer a quick question about your parts could be the difference between those parts running on time and the shop having to break down your setup to free up the machine—and then set it up all over again at a later date.
4. Streamline approvals
Approvals are a necessary part of any manufacturing process. Whether you need to greenlight a design iteration, a First Article Inspection, or anything else, have a clear process in place for getting quick approvals in your organization. That includes letting your manufacturing partner know who in your company is responsible for each approval so your shop knows where to direct their requests.
If you’re working with us and are local to our machine shop in Jacksonville, you can even stop by our facility for approvals to save time and money on shipping.
5. Work with a turnkey contract manufacturing services provider
When you need a part made from concept to completion, you have a couple of options. You could work with two separate vendors—one for engineering and another for manufacturing—or you could work with a turnkey contract manufacturing services provider that specializes in both.
At Polyhistor, we provide a comprehensive range of in-house capabilities—everything from initial product development services and rapid prototyping services to Low Rate Initial Production (LRIP) and final production.
When you rely on one partner for all aspects of the manufacturing process, your project naturally moves along more smoothly and efficiently. This option minimizes bureaucracy and allows for a more streamlined process that gets parts in your hands faster.
Ready to work with an all-in-one design and manufacturing company for your next project? Request a quote from Polyhistor, and let’s get going on your great idea!