Want to ensure a smooth manufacturing process the next time you request a quote?
Avoid common precision machining challenges by carefully designing your part, product, or prototype according to Design for Manufacturing (DFM) best practices.
Read on to learn Polyhistor’s tips for getting a top-quality product at the best possible price.
Polyhistor’s DFM Tips for Successful Precision Machining
Here are six precision machining challenges that can be solved with smart DFM:
1. Challenge: Thin structures
Does your part have thin walls or features? Delicate structures can easily warp during precision machining without adequate support from fixtures. The challenge is even greater when the entire part is thin—an issue we recently encountered at our CNC machine shop.
In this particular case, the customer asked us not to make any design modifications, which made their part costly to machine. But you don’t have to pay the (literal) price for a part with thin structures. Instead, consider one of these solutions:
Solution A: Add holes. Machining thin structures is easier when a part includes a few extra mounting holes. Additional holes allow us to use more supporting fixtures to stabilize the part during machining.
Solution B: Add features. If additional fixturing holes aren’t possible, our product engineering services team can help you design another feature or two that will serve the same purpose. In many cases, one simple add-on feature is enough to solve the problem.
It’s important to note that there isn’t a single ideal solution for machining a part with thin walls or features. Factors like the size of the part and the number of internal features are essential considerations when determining the best approach.
That’s why if your part has thin structures, we always recommend engaging Polyhistor for a design review before finalizing your design. We’ll identify any issues prior to machining and make recommendations before our machinists are on the clock.
2. Challenge: Deep holes
Traditional tooling isn’t ideal for drilling deep, narrow holes. For example, a 10” hole is 40x longer than the diameter of a standard ¼” drill, and it’s tremendously challenging to achieve a hole of that depth with accurate straightness.
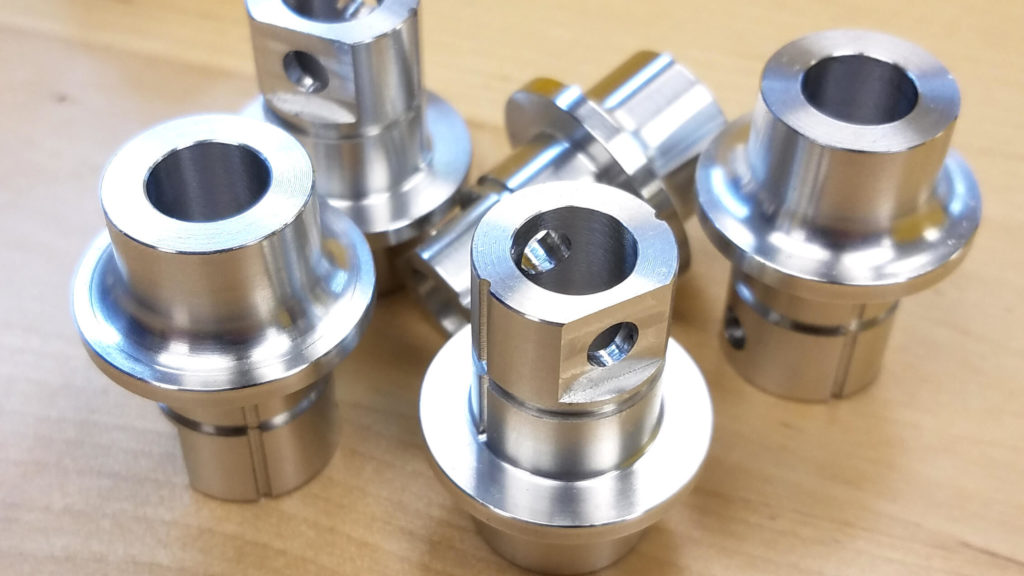
Solution A: Use drill fixtures. Depending on your part’s design, we may be able to apply drill fixtures to ensure straightness. But ask yourself: does the hole need to extend through the entire part, or can it be shortened? We’ve machined spray nozzles where only the final length of the hole required true straightness. Could these considerations apply to your part, too?
Solution B: Design around the deep hole. Designing a larger diameter for the deep hole or drilling it from a different direction can enable easier machining. Or approach your design with creativity, and you may be able to eliminate the deep hole altogether!
3. Challenge: Deep pockets
Like deep holes, deep pockets can be difficult to achieve with standard tooling. If particularly slender tools are required, the resulting vibrations can compromise your part’s surface finish. As if that weren’t enough, the tools required to machine deep pockets are often difficult to source, increasing costs and lead times.
Solution: Use a 5:1 ratio. When designing pockets, maintain a length to diameter ratio of no more than 5:1 so that we can machine the pockets quickly and affordably with our standard, in-house tooling.
4. Challenge: Incorrect material callouts
Occasionally, a customer will request a material grade or temper that’s especially difficult to machine. Some challenging material selections are unavoidable, but there are often opportunities to choose comparable alternatives.
For example, 6061-O aluminum alloy can easily be substituted with 6061-T6 for much simpler precision machining. Healthy communication between the engineer and the manufacturer can ensure the best material selection for each job.
Solution: Learn about your material needs in advance. Merely calling out “aluminum” for your part is unlikely to be specific enough, so it’s essential to identify your precise material needs before requesting manufacturing services. Even when the grade and temper of the material are machining-friendly, you should know with certainty that both are appropriate for your application.
For example, one customer requested that we manufacture their heat sinks using 6061 aluminum alloy. While 6061 was appropriate for heat conductivity, it wasn’t ideal for the necessary sand casting. A356 is typically used for sand-casted parts but doesn’t provide the same heat conductivity. After communicating in-depth with our customer to explain our concerns, we helped them select the best-suited material for their project.
5. Challenge: Undercuts
It’s not often that we see requests for undercuts, but when we do, these features always require careful attention. Using keyway or lollipop cutters, Polyhistor can handle almost any undercut request, achieving highly accurate recessed features that straight tools can’t access.
Solution: Keep your undercuts simple. An undercut can be incredibly challenging (and occasionally impossible) to machine when it envelops intricate features.
We recommend avoiding complex features within an undercut when possible. If such intricacies are needed, consult our product engineering services team before finalizing your design. We’ll help you identify the best method for achieving your part’s required features while maintaining machinability and cost-effectiveness.
6. Challenge: Square corners
Interior square corners are typically a design oversight. Round tools cannot form perfect right angles, meaning costly non-standard tooling and extensive machining time are required to create sharp corners.
Solution: Avoid or adapt. To solve this challenge, you can avoid designing interior right angles altogether or include a tiny channel tag or “earmark” at the corner. The channel tag allows a square mating part to fit neatly into the corner. You may even choose to fit a fastener into the earmark!
Polyhistor Provides Product Engineering Services with DFM Guidance
If you have any questions about the manufacturability of your design, Polyhistor is here to support you. Our team is committed to providing the DFM guidance necessary to ensure superior quality parts and products at a reasonable price. Get a quote today!