Aluminum is second only to steel in popularity, and it’s easy to see why! Pure aluminum is plentiful, comprising 8% of the Earth’s crust. In its many alloyed forms, aluminum’s unique properties make it a top choice for a wide range of industries and applications.
Let’s explore further.
Advantages of Aluminum in Manufacturing
At Polyhistor, we call aluminum a “feature-rich” material because of its versatility.
Due to its low density, aluminum is perfect for applications with strict weight limitations. Aluminum alloys are notably stronger and more dimensionally stable than many other low-density metals.
The dimensional stability allows for impressively fast machining. Thanks to the easy machinability, we can often offset the price of the raw material with reduced machining costs. Aluminum is also suitable for tight tolerances, thin walls, threading, tapping, and the full range of sheet metal fabrication services.
Naturally corrosion-resistant and thermal-conductive, aluminum performs reliably in even harsh environments.
Aluminum Grades
You can identify aluminum alloys and their primary alloying elements simply by looking at the series number:
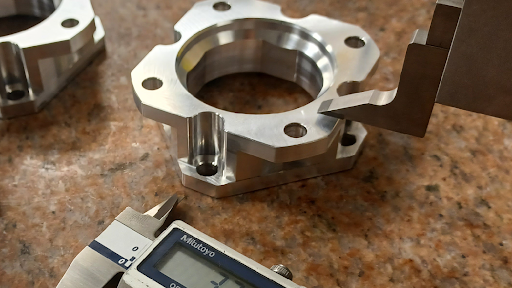
- 1000 series: 99%+ pure aluminum
- 2000 series: aluminum/copper alloy
- 3000 series: aluminum/manganese alloy
- 4000 series: aluminum/silicon alloy
- 5000 series: aluminum/magnesium alloy
- 6000 series: aluminum/magnesium/silicon alloy
- 7000 series: aluminum/zinc alloy
6061 aluminum
Polyhistor clients most commonly request 6061 aluminum, which has these mechanical properties:
- Good corrosion resistance
- Good weldability
- Good machinability
- Good anodizing response
Primarily alloyed with magnesium and silicon, 6061 aluminum comprises 97.90% Al, 0.60% Si, 1.0% Mg, 0.2% Cr, and 0.28% Cu.
Plate and extruded forms of 6061 aluminum alloy are particularly popular with our aerospace clients, who value this material’s strength, atmospheric corrosion resistance, and machinability.
7075 aluminum
When clients require aluminum with increased strength, we recommend 7075 aluminum, with its 2.81 g/cm³ density. The mechanical properties are as follows:
- Poor corrosion resistance
- Poor weldability
- Fair machinability
- Good anodizing response (which makes up for the poor corrosion resistance)
Primarily alloyed with zinc, 7075 aluminum comprises 90.00% Al, 5.60% Zn, 2.50% Mg, and 1.60% Cu.
Another aerospace favorite, 7075 aluminum is found in airplane wings and fuselages as well as in recreation equipment used by bicyclists, rock climbers, archers, and marksmen.
MIC-6® aluminum
We recommend MIC-6, a 7000-series cast aluminum tooling plate, when parts require enhanced dimensional stability.
This fully stress-relieved, free-cutting aluminum/zinc alloy arrives in our shop with a surface finish of 20 RMS or better, a thickness tolerance of +/- 0.005”, and dual-sided PVC protection. The continuous cast process used to produce MIC-6 makes it highly resistant to distortion and temperature changes.
MIC-6 aluminum offers these mechanical properties:
- Good corrosion resistance
- Good weldability
- Excellent machinability
- Fair anodizing response
MIC-6 is ideal for applications with precision tolerances and intricate dimensions. Polyhistor frequently uses it for tooling, fixtures, molds, and more.
Additional aluminum grades
Whatever your requirements, Polyhistor can procure an aluminum alloy with the chemical, physical, and mechanical properties you need. We frequently rely on aluminum selections with these designations:
- For cast applications: A356, A380
- For sheet metal fabrication applications: 5052, 3003
- For sand cast applications: A356, A380
Precision Machining Considerations
Polyhistor’s CNC machining services experts have the skill to manufacture superior quality parts from even finicky alloys.
Workholding is a top consideration when machining aluminum because of the material’s relative softness. We carefully control the torque during machining so we don’t inadvertently over-tighten the aluminum workpiece and cause it to warp, a particular concern when machining thin walls and fine features.
Aluminum in Defense Machining
Polyhistor’s defense industry clients are our most prolific aluminum users. With stringent requirements for lightweight parts with high structural integrity, these clients rely on the full spectrum of aluminum alloys to achieve top-quality parts and products for simulation, communication, and other applications.
Balancing Cost and Strength
Though the cost of aluminum is higher than that of its more popular counterpart, steel, aluminum is significantly more machinable. Because we can machine aluminum so much more quickly, the costs tend to break even; sometimes, we can even make aluminum parts for a lower cost than making the same parts from steel!
To determine whether your job is better suited to aluminum or steel, you’ll want to evaluate the material and machining costs against your project’s strength requirements.
Are your parts destined for a high-strength application? Should they have high vibration tolerance? Do you anticipate material fatigue issues?
Together, let’s first assess your application and determine the right approach for both cost-effectiveness and performance.
Finishing and Environmental Considerations
A part’s surface finish is another key consideration, and it’s directly tied to the application’s operating environment. Parts that will be exposed to moisture, extreme temperatures, or heavy use will have different requirements than light-use parts in a dry, temperature-controlled environment.
Finishing processes such as anodizing, powder coating, wet painting, and military-grade CARC painting can improve chemical resistance and other properties.
Of course, some surface finishes may impact a part’s dimensions—a legitimate concern for parts with critical tolerances. Powder coating, for instance, adds a small amount of thickness to the surface of a part, which can throw parts out of tolerance and cause assembly issues further down the line.
A quick conversation about your surface finish needs will allow us to determine the best path forward.
Polyhistor Prioritizes Client Consultations
All of us here at Polyhistor value the opportunity to provide guidance on every aspect of your production, from material selection to CNC machining services to secondary processes. Our engineers will evaluate your design and make recommendations based on production quantity, turnaround time, cost reduction, and, of course, the final application.
For example, some aluminum jobs benefit from near-net extrusions or castings to reduce machining time and slash costs. Talk with the Polyhistor team, and we’ll guide you in the right direction.
Whatever your aluminum machining needs, we’re here to help!