Even low-volume productions of high-mix parts require workholding, but machining custom jaws for a short production run is almost never efficient or cost-effective. By utilizing modular vise systems in place of custom jaws, our precision machine shop can keep production times short and costs low.
Some shops shy away from the upfront expense of modular vise systems, but at Polyhistor, we’re committed to delivering high-quality parts quickly and affordably—and ADAPTIX™ modular vise systems by Norgren allow us to honor that commitment for even the smallest orders.
What Are Modular Vise Systems?
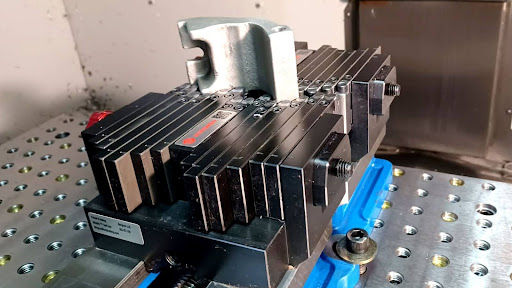
A modular vise system is a versatile clamping solution that can be easily adapted to various workpiece shapes and sizes. This adaptability is particularly beneficial for lower-volume productions for which it isn’t time or cost-efficient to create custom-made jaws. Our precision machine shop uses modular vises and fixture plates to pre-configure part setups, leading to faster and more efficient part changes.
Modular Workholding Improves Costs and Lead Times
The main advantage of modular workholding systems is that they streamline the manufacturing process. We focus on maximizing each CNC machine’s “spindle time”—the duration a machine is actively working. The faster we can complete setups and switch out parts, the more we enhance machine utilization, which translates to direct cost savings for our customers.
Tooling costs (which include fixturing), particularly for small jobs, are a significant expense in CNC machining from Jacksonville, Florida, to Jackson, Wyoming. By employing modular vise systems in place of custom jaws, we can reduce most customers’ setup costs by an average of 50%!
Though investing in a modular workholding system can cost several thousand dollars, and custom jaws can be made for a mere $50 in materials, the higher upfront investment is undoubtedly worthwhile. Over time, the speed enabled by modular workholding can play a powerful role in a precision machine shop’s success by allowing it to produce more parts in less time.
Polyhistor’s Strategic Use of Modular Vise Systems
Polyhistor’s modular systems have proven to be a game-changer for customers requiring low-volume, high-mix parts. We can begin a new production with a modular system and then transition to custom jaws as your production volumes increase. This flexible approach allows us to adapt to every customer’s evolving needs, ensuring cost control and timely delivery even during the ramp-up phases of production.
Limitations and Adaptations
Modular vise systems are ideal for irregularly shaped parts, so we often use our modular workholding in the second operation of machining after we’ve cut the workpiece into an irregular shape.
Modular vise systems do have limitations, however. For instance, we typically avoid using them on workpieces made from softer materials, like plastics, due to clamping difficulties.
When machining plastic, we still have the option to leverage our 3D printing capabilities and print custom jaws that won’t damage the plastic parts, ensuring the same production and cost efficiency you receive for metal part orders.
The Polyhistor Edge
We’re honored to be one of the top prototype companies in Florida, and we credit our modular workholding systems for helping us maintain our reputation for fast innovation and customer satisfaction.
Our problem-solving mindset underscores our promise to provide on-time, cost-efficient solutions that never compromise the quality of your parts. By reducing fixturing costs, increasing machine utilization, and minimizing setup time, modular vises and fixture plates provide meaningful advantages over custom workholding.
When precision and efficiency are key, Polyhistor ensures the best possible outcomes. Whether you’re seeking small-scale production or a gradual move to larger volumes, you can count on our precision machine shop to deliver exceptional value every step of the way.