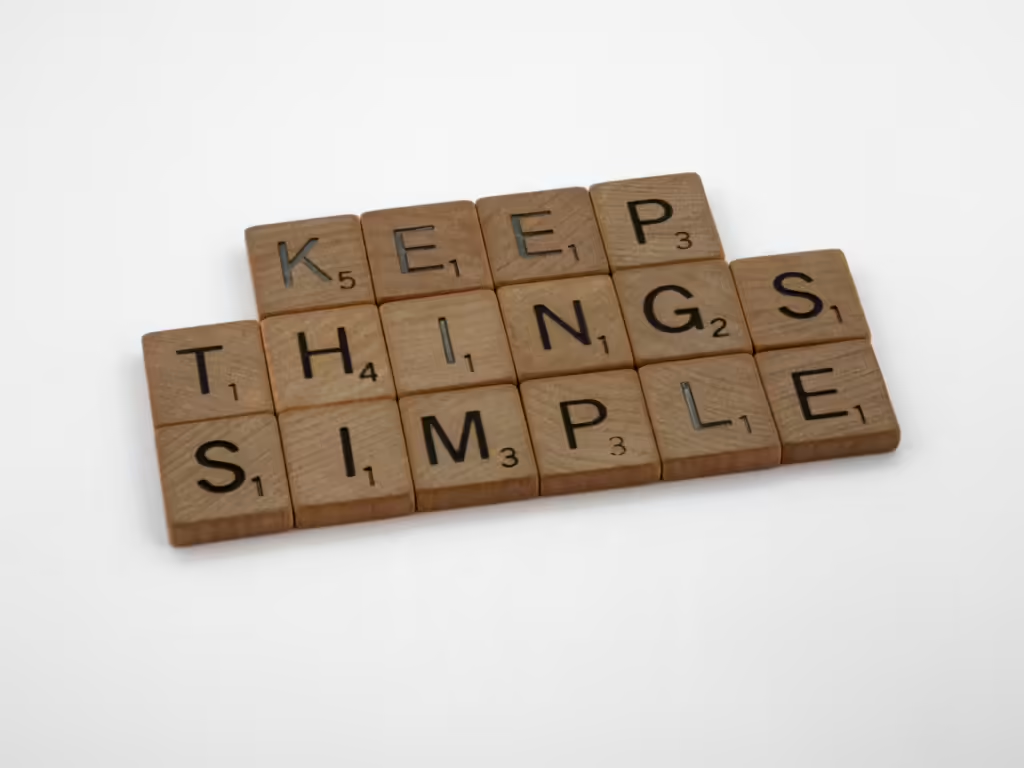
There are tremendous opportunities to reduce manufacturing costs for almost every project. The key is to consider and implement cost-saving strategies as early as possible—beginning with engineering design.
Keep It Simple: Cost-Saving Product Design Tips
Much of the cost to manufacture a product is directly related to how it is designed, assembled, and packaged. Polyhistor’s biggest piece of advice during the design phase is this: keep it simple. Here are a few tips for reducing complexity and, in turn, costs.
1. Use as few parts as possible
Remember this Design for Assembly rule of thumb: the more parts that make up a product, the higher the cost. Minimize the number of parts in an assembly as much as you can. When many parts are required, consider making the parts screw or snap together with minimal effort to reduce assembly costs.
2. Consider a modular design
Think ahead about your product’s lifecycle. Will certain parts require maintenance or eventually need to be replaced? If so, a modular design will enable you to easily remove and replace different modules throughout the product’s lifecycle.
3. Use standard components and materials
There’s no reason to custom-make a screw when there’s a perfectly good one you can purchase off the shelf for much less money. A similar logic applies when selecting materials. Don’t choose an exotic material that’s costly to source and machine when a standard material can serve you just as well.
The Value of Contract Manufacturing Services
While engineers can implement many product design tips independently, some cost-saving strategies aren’t apparent without the support of a manufacturing partner.
When Polyhistor partners with customers to provide contract manufacturing services, we help them think about opportunities for cost savings they might not otherwise have considered.
For instance, you may not realize that seemingly inconsequential design choices, like the location of an “on/off” button, can significantly impact the cost of your project. When you involve Polyhistor early in the process and communicate with us about your design, we can inform you that changing the location of that “on/off” button will save you $5,000 in tooling costs and $4/part.
Shipping and packaging are other important considerations that engineers tend to overlook. Polyhistor can make sure your parts and products are designed with standard shipping pallet sizes in mind to help you save money on shipping costs. When it comes to packaging, we may recommend sustainable options like reusable packaging to further reduce costs.
All these small details contribute to your overall costs. A contract manufacturing services partner like Polyhistor will consider them so you don’t have to.
When you partner with us early, we can have an upfront conversation about your budget to help you determine if it’s appropriate for your requirements. Then, we can discuss all the options together and collaborate on the best solutions.