Does your next project require electrical engineering, prototyping for electrical components, or electromechanical assembly? With Polyhistor’s advanced product engineering services, your ideas come alive as tangible, superior-quality products.
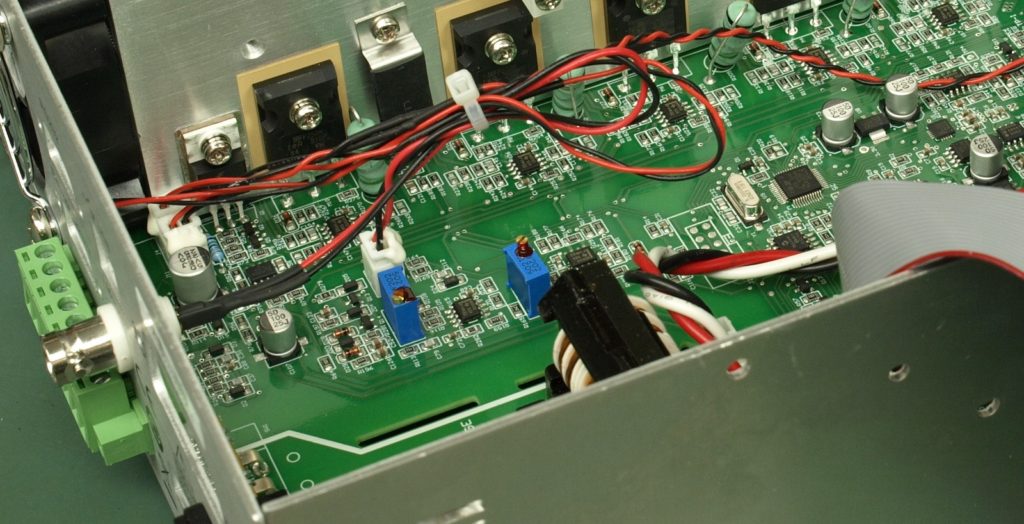
While nothing in the manufacturing world is truly simple, electromechanical parts and products introduce a unique layer of complexity to precision machining. Electromechanical prototypes, for example, tend to require a minimum of three revisions—and often many more—before achieving a customer’s minimum viable product.
To ensure successful electromechanical product development and manufacturing, we’ve outlined a series of best practices.
Best Practices for Electromechanical Parts and Products
We didn’t invent these best practices because we were bored on our lunch break. Each of these guidelines stems from Polyhistor’s real-world manufacturing experience. If you incorporate these tips into your product planning workflow, we’re confident you’ll reap the rewards!
1. Design with supply chain availability in mind
You’re likely already familiar with Design for Manufacturing and Design for Assembly—concepts that drive successful end results from the first stages of product design. But have you heard of Design for Supply Chain Availability?
No?
Neither had we—until now!
The idea of designing for supply chain availability is to keep the supply chain status in mind throughout your design and development process. This consideration is especially critical in our post-COVID world, as many electronic components are still in short supply.
Before working specific components into your design, investigate each component’s availability. If you’ve chosen Polyhistor as your partner in product engineering services, we can help you evaluate component availability and select substitutes where necessary.
2. Provide detailed product requirements
The further you advance along your product development roadmap, the harder it is to change course—especially when developing electrical components. To facilitate a successful end product with as few “bumps in the road” as possible, you’ll want to provide these details to your manufacturing partner:
- The application in which your product or component will be used
- The target functionality of the product or component
- The user interface that will enable communication between your product and its user
If your project is still in the electrical prototyping phase, you’ll find that it’s easier to communicate your requirements than to define specific components. By leaning into the former versus the latter, you grant your manufacturing partner the flexibility to select the best parts for your project.
You’ll also benefit from improved quoting accuracy when your product developer understands the full scope of your project, from concept to creation.
3. Shamelessly share your production budget goals
Nobody benefits from keeping secrets (unless you’re throwing us a surprise party, in which case: what time should we show up?)
Be transparent with your contract manufacturer about your production budget goals, and prepare to have an honest conversation about how to reasonably work within that budget. In most cases, your manufacturing partner will be able to accommodate budgetary constraints, even if your pricing target is aggressive.
Collaborate with them to identify opportunities to cut costs while still achieving your product’s primary goals. Even if some of your requirements leave little room for saving money (such as meeting military specifications for aerospace components), you’ll benefit from communicating candidly about your budget for development and product engineering services.
4. Test, test, and test again
It’s not enough to take your electromechanical component “for a spin” before launching the design into production. Appropriate product testing is absolutely necessary for ensuring the proper functioning of any component. Testing is even more important when electronics are involved because so much more can go wrong!
Not convinced?
Without testing (or with inadequate testing), your component could enter production only to encounter a product failure that ultimately costs tens of thousands of dollars to remedy. We’ve seen it happen, and we’d never want it to happen to you.
Polyhistor can help facilitate the testing cycles needed to verify a prototype’s electromechanical functionality with a series of methods:
- Schematic diagrams. A schematic diagram depicts a system’s elements using graphic symbols to demonstrate each component’s location and behavior. Schematic diagrams typically act as the first visualization step when designing electromechanical components.
- Breadboards. Also called protoboards or terminal array boards, the solderless breadboard enables electrical connections via a grid of spring-loaded clips. Since breadboarding is a solderless, non-destructive process, breadboards are reusable. Though they only function with through-hole components, breadboards are a reliable next step toward verifying an electromechanical design.
- Printed circuit boards (PCB). This crucial electromechanical design step is a low-cost testing method for surface-mount components, using printed circuit boards with conductive tracks to connect the components. PCBs offer an excellent way to test your product’s circuitry without expensive wiring.
- Raspberry Pi and Arduino. Popular prototyping platforms that enable quick and easy circuitry testing, these development boards aren’t efficient when testing at scale. If your manufacturing partner utilizes one of these development boards, you’ll likely only encounter them during prototype demos.
Polyhistor Pro Tip: Building Is Harder than Buying
Just because you can walk into a consumer electronics store and buy an electromechanical product for fifty bucks doesn’t mean it is low-cost to develop. The economies of scale divide the engineering development into a small fraction of the price tag. Choose to invest in a product engineering services partner who can help you navigate the complexities of electromechanical design and deliver a finished product you can be proud of!
We’d be honored for you to choose Polyhistor as that partner.
Request a quote to work with us.