Let’s assess how to go about selecting a plastic for your part and examine the factors engineers should consider during the design process.
Selecting a Plastic for Your Part
Not all plastics are created equal, so you should familiarize yourself with the characteristics of common plastics before determining which material is best suited for your project.
Know your plastics
- Will the part be exposed to the elements?
- Will it operate in extreme temperatures?
- Will it be used in a wet environment?
- Will it need to conduct electricity?
- Will it need to be friction-free?
If these questions seem excessive, consider how high-performance plastics are used: in heavy machinery, in Department of Defense projects, for wear plates in construction equipment, and in other critical applications. It’s important to make the right selection.
For most projects, Polyhistor uses one of three premium plastics:
- Delrin® (acetal)
- Nylon
- UHMW
Whether you’ve requested one of these common high-performance plastics or a more obscure material, Polyhistor can help you obtain top-quality parts without blowing your budget.
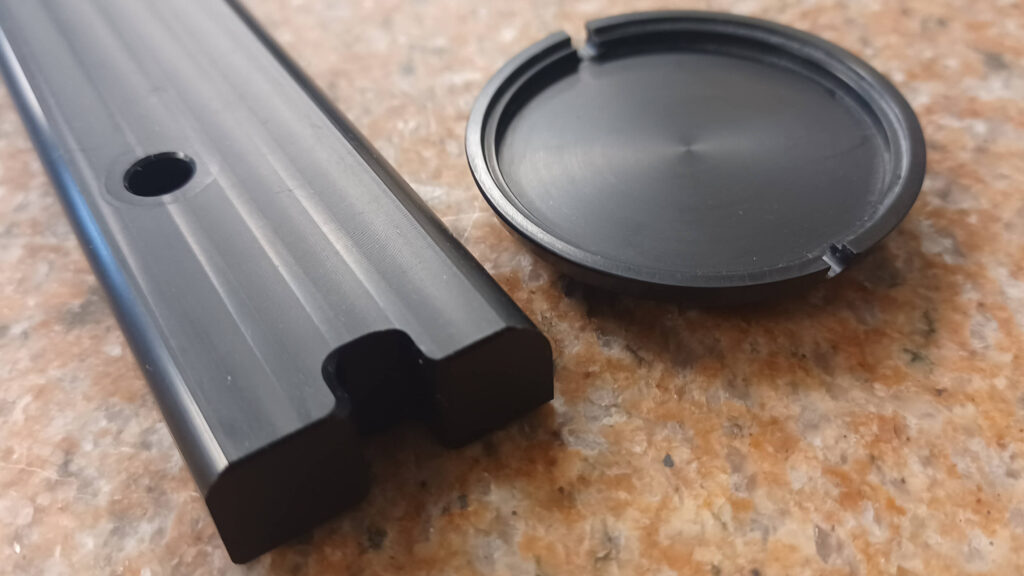
Compare aluminum vs. plastic
If you’re evaluating the benefits of aluminum vs. plastic, there are two factors to consider:
As custom manufacturing experts who provide plastic machining services, we’re deeply familiar with the challenges of working with polymers.
Though all materials embody unique characteristics that must be considered throughout the design and machining processes, plastic’s idiosyncrasies stand out. Unlike metals, for example, plastic can be impregnated with oil or glass to enhance wear resistance or strength.
- Material weight. How much should the finished part weigh? Can you achieve that target weight with the material you’ve chosen?
- Cost. Don’t fall for the common misconception that plastic materials are always less expensive than aluminum or other metals. While some plastics are quite cheap, others are very costly. If you’re trying to stick within a specific budget, talk to our team about which material best suits your project and price point.
Leverage plastic’s potential
Did you know that nylon plastics can be dyed? Polyhistor dyes nylon in-house, offering a range of neutrals from white to black and everything in between. We’re also capable of achieving bold colors with richly toned fabric dyes.
Request dyed nylon to:
- Complement brand colors
- Make it easy to locate a specific part in an assembly
- Produce an aesthetically pleasing part or product
- Avoid the need for painting or coating your part or product
3 DFM Tips: Designing for Plastic Machining Services
Because plastics are more pliable than metals, they shift more easily during machining. This movement can hinder accuracy and repeatability—never an ideal situation!
But you can combat plastic machining challenges by adhering to three key Design for Manufacturing (DFM) recommendations.
1. Avoid thin features
Machining thin features in a plastic workpiece is a tedious, complicated process. Holding tolerances can be nearly impossible, and the material is likely to warp.
Thin walls, in particular, can pose a challenge—especially if they are deep. For example, thin walls that are 2” deep are more prone to weakness than thin walls that are only 0.25” deep.
2. Don’t over-tolerance your part features
Exceedingly tight tolerances can be quite difficult to achieve when machining plastic. When tight tolerances are absolutely necessary, we’ll gladly develop a solution. However, if your part doesn’t require precision tolerances, you’ll save time and money by calling out standard tolerances instead.
3. Design counterbores, not countersinks
Because countersinks rely on pressure to secure a fastener, counterbores are a better option in plastic parts. A countersink may be well-fitted at first, but in mere weeks or even days, the hold might be too loose. A counterbore, on the other hand, is much less likely to rattle loose.
Make Polyhistor Your Preferred Partner for Plastic Machining Services
Polyhistor is more than a precision machine shop. Our engineers also provide product design services and can help you select the right polymer for your parts. Talk to our team about your upcoming plastics project, and we’ll work with you to perfect your design for exceptional manufacturing results.