Many of our customers are familiar with Polyhistor’s engineering experience and expertise as a precision machine shop. However, we also like to highlight some of the smaller things they may not realize about Polyhistor. We are excited to showcase our reusable packaging, our waste reduction efforts, and the subtle but significant benefits these initiatives offer to our customers.
How We Reuse Packaging
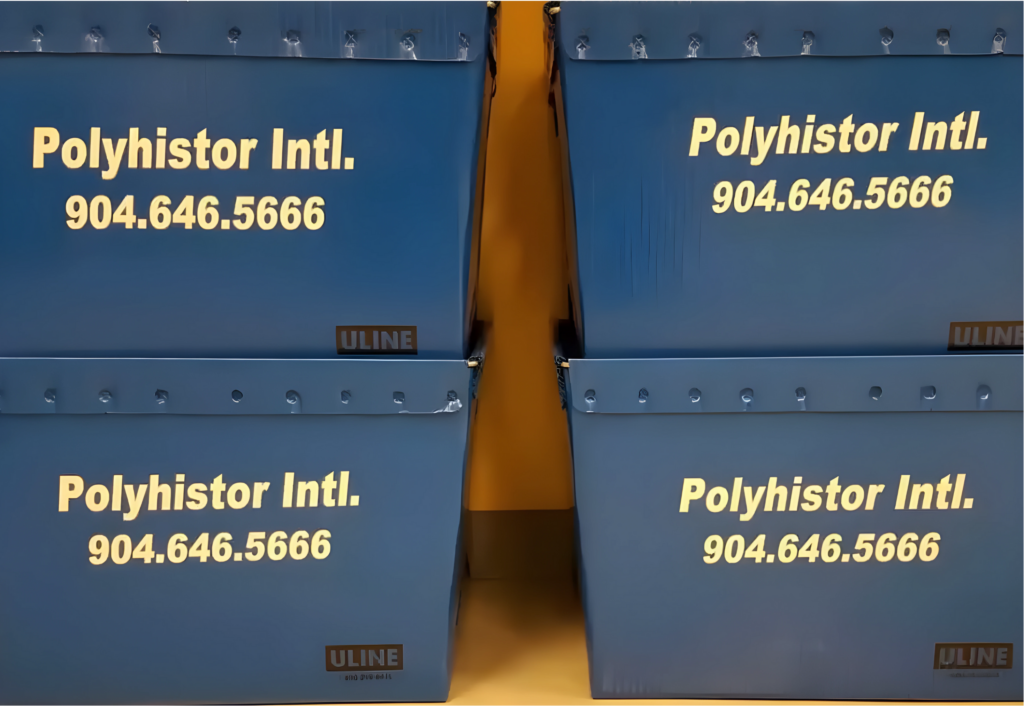
Decades ago, when we first started receiving repeat orders for the same parts, we came up with an idea. Why not find packaging for these customers that we could reuse for every shipment, rather than using the same disposable packaging as we did for other customers? Using a new cardboard box for every shipment of the same product to the same customer created unnecessary waste, so we got to work on a solution.
We now opt for reusable packaging whenever possible, which lasts for many years for repeat shipments. For most of our repeat customers, we have corrugated boxes that we fit with custom-made foam inserts. These spacers fit these repeat parts snugly, reducing the risk of damage compared to a typical delivery. We also have these hand delivered by a courier further ensuring the safety of the products.
When we work with platers, we also recycle packages. We don’t use the corrugated boxes with years of potential reuse, but we do use the same packaging back and forth with our platers about a dozen times before it’s no longer usable. At that point, it goes into a typical recycling waste stream.
How This Attention to Detail Benefits Polyhistor Customers
In everything we do, we aim to be as sustainable as possible and reduce waste. There is an environmental motivation, of course – we hope to do as little harm to the environment as is feasible for our business. But there are also practical benefits to sustainability: the more we minimize waste and reduce costs, the better pricing we can offer customers.
With a move like reusable boxes, it’s true that such a decision alone won’t too drastically slash our customer’s prices on offerings like CNC machining services. But this attention to detail extends beyond packaging. The philosophy has a huge effect on our overall output, both in terms of pricing and quality. We are focused on every part of our process to make sure we are offering the best product possible, down to our thoughtful shipping practices.
The packaging doesn’t only save on waste, it boosts the customer experience, as well. It’s part of our bigger customer-centric approach to manufacturing. Many of our customers have remarked to us how much they prefer removing parts individually from the custom spacers, rather than having to unwrap them from the typical paper that is used to protect parts in shipping situations. These kinds of compliments on the pleasures of working with Polyhistor mean a lot to us.
Attention to detail is part of everything we do at Polyhistor. Contact us to request a quote and learn more about how we can help you.