Are you considering injection molding for your next project?
Injection molding, which consists of injecting molten material into a mold and allowing it to harden, is an excellent solution for high-volume or mass-produced quantities of identical parts.
While the upfront cost of tooling for injection molding is more expensive than conventional machining, an initial investment can lead to long-term savings for the right parts. The fully automated process allows for a shorter cycle time than conventional machining, as well as less material waste and minimal secondary operations (if any).
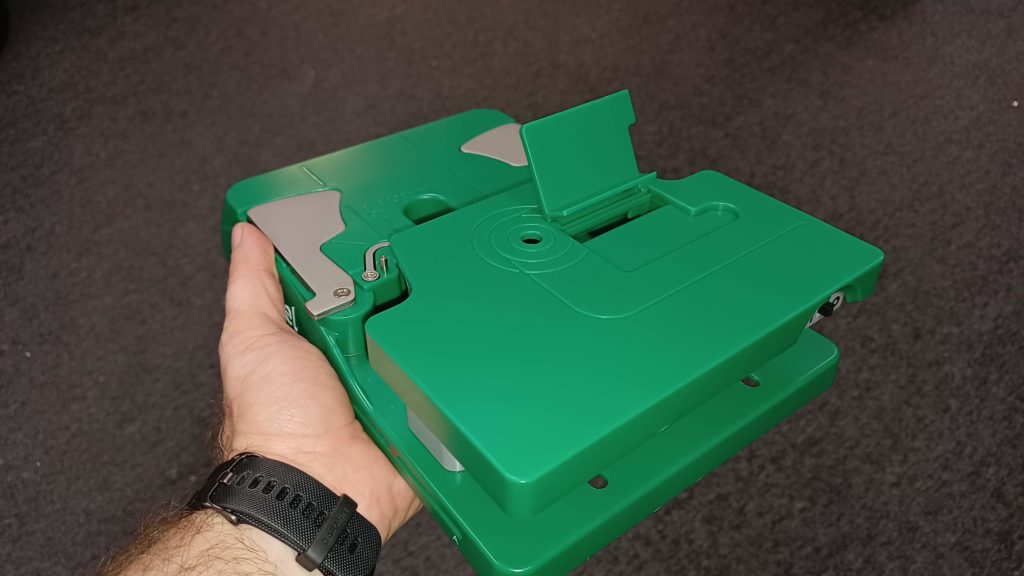
There are, of course, limitations to this manufacturing method—especially if you’re planning a transition from 3D printed prototypes to injection molded parts. Some 3D printed part features are too detailed or geometrically challenging for injection molding. And if your part requires customization or personalization, 3D printing allows for the flexibility to produce variations of a part on-demand.
If you’re all in on injection molding for your next project, keep in mind that designing for injection molding is different from designing for CNC machining or 3D printing. Here are several important design tips to consider:
7 Design Tips for Injection Molding
1. Start with your end goal in mind.
In the manufacturing industry, the real money is in production. Even if you’re just starting out with a prototype, consider the production method you plan to use and design your part for that method specifically.
If you’re partnering with a company for product design services, make sure everyone is on the same page about this approach.
2. Consider draft angles.
Ever notice how most cake pans don’t have true 90 degree angles in the corners? That’s because it’s next to impossible to remove the cake from such a pan without it getting stuck.
This same principle applies to injection molding. If your part has a heavy surface texture, you’ll need a larger draft angle to help release it from the mold. If your part has a smooth or mirror finish, on the other hand, a smaller draft angle is sufficient because the part will release easier from the mold.
3. Avoid parts or features that are too thick.
During the injection molding process, thicker features cool at a different rate than thinner features. Inconsistent cooldown rates can lead to issues like uneven shrinkage, divots, and shrink marks.
These problems are common for ribbed parts, which are prone to what’s known as sink marks if the rib is too thick.
4. Avoid parts that are too thin.
When parts are too thin, there’s a risk of the material penetrating the mold and flowing out. Making a part thicker is an easy fix, but some applications don’t allow for a thicker design.
One innovative solution to this problem is to ultrasonically weld a separate thin part onto an injection molded part.
Another solution is to choose a material that flows better. The key here is to work with your mold maker early on in the process. They can help identify the necessary pressure and mold temperature to keep your part intact.
5. Insert hardware after injection molding.
Using a hybrid manufacturing approach, it’s possible to incorporate threaded inserts, heat set inserts, and other metal parts into an injection molded part as a secondary operation.
6. Develop a plan for undercuts.
If your part has recessed surfaces that are inaccessible with a standard tool, you have a couple of options: 1) use a special tool to remove the part from the mold or 2) design around the undercut.
Using special tooling can increase cost and cycle time, so designing around an undercut is usually the preferred solution.
7. Get creative.
Did you know that car parts that look like leather come right out of the mold that way? With injection molding, you have the liberty to design multiple surface textures into one part, or even create a part that looks and feels like another material.
Consider the finish of your injection molded part early on in the product development process to plan for the right material.
Finally, choosing the right partner for injection molding is critical. At Polyhistor, our team has decades of experience managing injection molding projects for our customers.
We work with a reliable network of well-vetted molders to deliver high-quality parts—including local manufacturers near our Jacksonville machine shop to ensure that defense parts are made in the USA. We also offer in-house product design services to optimize designs for injection molding.
Contact us to discuss injection molding for your next project!