According to the American Ceramic Society, the oldest known ceramic artifact is dated as early as 28,000 BCE. Indeed, humans have been manufacturing and using ceramics since ancient times.
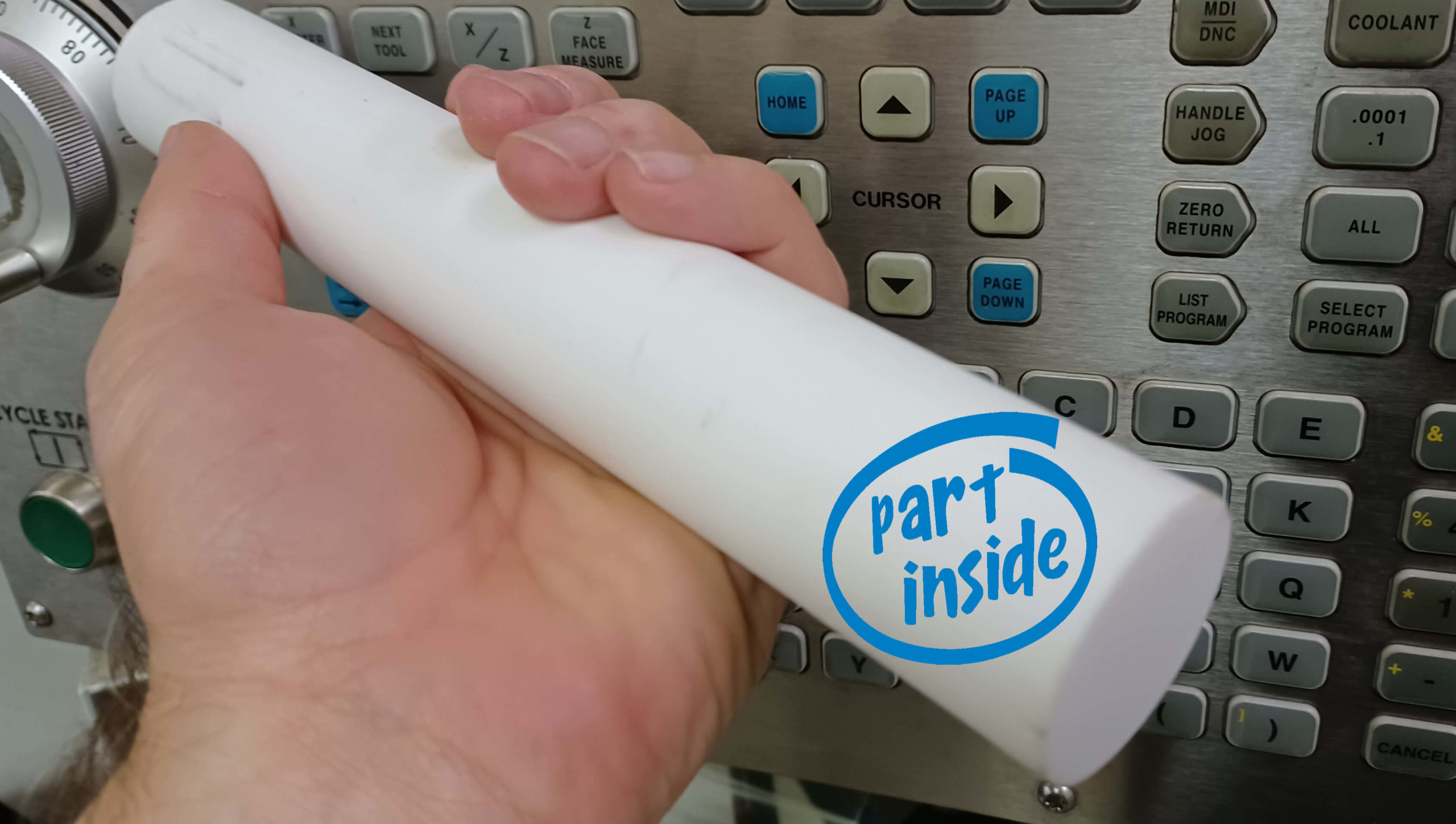
Ceramic applications have evolved substantially over the last 30,000 years. These days, the material is used in everything from bricks for building houses, to kitchen knives, to brakes on vehicles, and even in bulletproof vests.
Perhaps you’ve never considered ceramic material as part of your product development plans. On the other hand, maybe you know you need ceramic for an upcoming project, but you’re unsure of the next steps. Either way, here are five key considerations for CNC machining for ceramic applications.
5 Key Considerations for Machinable Ceramics
1. High heat tolerance
Ceramics are excellent insulators of high temperatures, and therefore ideal for applications that must be able to withstand extreme heat. This information comes as no surprise when you consider the use of primitive clay ovens long ago and even modern-day Big Green Eggs that people use to smoke meat in the backyard.
2. Low thermal expansion
Ceramics are also known for their low thermal expansion properties. When contrasted to a material such as aluminum, which can expand as much as 2.5 mm at high temperature differences over a span of one meter, ceramic parts are capable of maintaining their original shape more closely, ensuring a precise fit.
3. Non-conductive
Ceramics resist the flow of electricity and have long been the material of choice for electric insulators. For certain parts where it’s difficult to integrate electrical insulation material into the part’s existing material, a substitute to a ceramics may offer a viable solution. The material also serves as a reliable layer in parts requiring electrical insulation.
4. Corrosion resistant
Ceramics are extremely corrosion-resistant, giving them a distinct advantage over many metals that are vulnerable to corrosion over time or if exposed to oxidizing substances.
If your part will be exposed to harsh environments (e.g., being submerged in seawater) which can cause significant corrosion, you may want to consider incorporating ceramic materials into your product design.
5. Prone to brittleness
For all of the wonderful qualities of ceramics, physical flexibility is not one of them. Ceramics are an inherently brittle material—but there are ways around this drawback.
Selecting a ceramic material with a homogenous composition, for example, ensures minimal brittleness. It’s also possible to work around brittleness during precision machining. The right CNC machine shop will know the correct way to approach ceramic machining. Just ask us.
Machining vs. Casting Ceramic Parts
You may be wondering if it’s better to manufacture your ceramic part using CNC machining or casting. The answer depends on two primary factors: volume and part complexity.
Generally speaking, if you’re dealing with high-volume production quantities, casting is the best option. On the other hand, if you only need a small amount of ceramic material, CNC machining can provide tighter tolerances and a better surface finish for a smaller upfront investment.
Part complexity is a more nuanced conversation, as many factors determine how difficult a part is to manufacture. At Polyhistor, we are happy to assist in designing and manufacturing ceramic parts.
If you’re wondering how to incorporate ceramics into your product design, we can help you evaluate the relevant factors as part of our product design services. If you’re trying to decide between machining or casting, we’ll provide a recommendation on which process is best for your application. We’ll then manufacture your ceramic parts to the highest quality standards.
Contact us today to discuss ceramics for your next project!