At Polyhistor International, our decades as a defense supplier have taught us the challenging conditions mission-critical equipment will face. Products must perform equally well in the scorching desert and frigid Alaskan conditions alike, all while maintaining sealing and protection.
When we manufacture defense-grade enclosures in our CNC machine shop, we’re creating shields to protect critical electronic systems in demanding environments. Find out how Polyhistor ensures our enclosures meet the rigorous standards of defense applications while maintaining cost-effectiveness.
The Extreme Performance Required for Defense Enclosures
Defense contractors demand certain performance characteristics for specific applications, each critical to success. Here are some of the key requirements that drive our precision machining for enclosures:
Environmental Protection: There are countless environments an enclosure must be prepared to withstand. Our enclosures meet your required ingress protection (IP) rating, whether it needs to be watertight for rain or submersible for underwater operations.
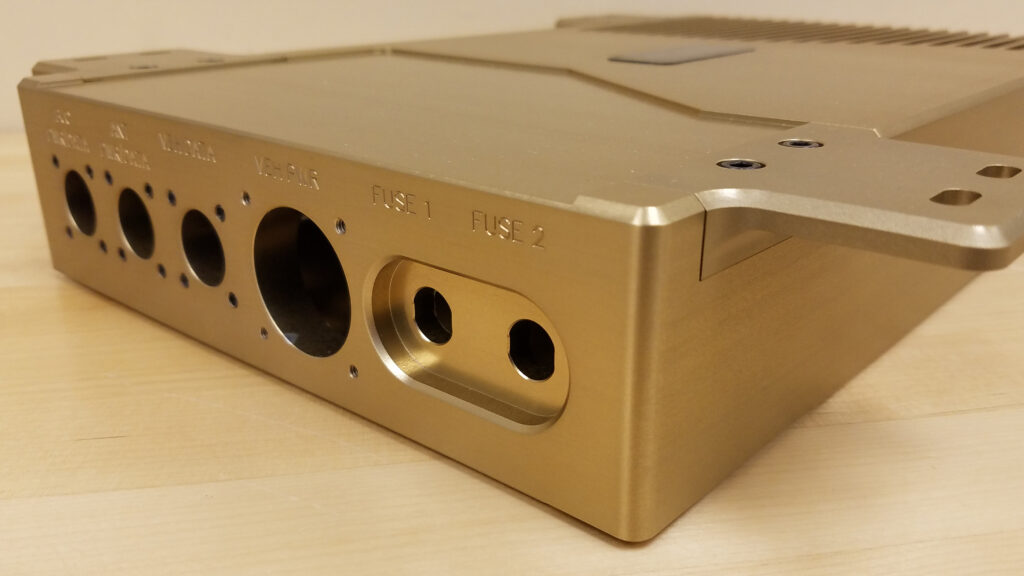
Electromagnetic Interference (EMI) Protection: EMI protection is crucial for safeguarding the sensitive electronics inside of defense enclosures and other defense products. We consult our partners on preferred EMI-shielding techniques, and our enclosures often incorporate specialized gaskets and materials to create a secure barrier.
Physical Durability: Defense equipment must survive extreme physical stress, from high-altitude airdrops to ground vibrations. We help you select proper materials and efficiently manufacture optimal features and structural integrity under high stress.
Thermal Management: Defense enclosures often hold powerful electronics that can generate intense heat. We can incorporate features such as heat sinks and cooling fins to ensure proper performance.
Our Design Expertise in Defense Manufacturing
The challenge in defense manufacturing isn’t just meeting performance requirements—it’s doing so efficiently and cost-effectively. Parts may look perfect in CAD, but the manufacturing required may lead to higher prices that could be avoided.
At Polyhistor International, we are ready to offer guidance on design for manufacturing and design for assembly for enclosures. As an ITAR-registered manufacturer specializing in simulation, training, and communication equipment, we offer product development services to help defense contractors avoid common pitfalls such as.
Complex surface finishing requires extensively customized masking, increasing both lead times and costs. By collaborating closely with our surface finishing partners, we find small design changes to improve manufacturability by simplifying masking.
Weight reduction is critical for certain applications but requires careful consideration. Lighter components can improve performance, but excessive material removal leads to long machining time and higher costs. Our team can help you find the best balance of weight savings and manufacturing efficiency.
Tight tolerances are often strategically necessary, but we always discuss designs with customers to determine when tight tolerances are truly critical. For example, we recently helped a defense customer replace solid pins with spring pins in their enclosure design, maintaining functionality while reducing manufacturing cost.
Leverage Our Experience and Expertise
We have manufactured defense enclosures for more than a decade now in our Jacksonville machine shop—but they’re far from our only defense parts. No matter your project, we can help you to develop parts that balance protection with practical manufacturability.
Our experience in partnering with the defense industry ensures you receive the highest-quality equipment while meeting your budget and timeline requirements.
Request a quote today to let us help you protect your mission-critical equipment!